EXtreme Composite EDGE …
Diese EDGE 540T stand schon einmal in meinem Modell-Hangar. Mit 2,6 Metern Spannweite war sie noch gut zu transportieren und handlich auf dem Flugplatz. Zudem waren die Flugeigenschaften super. Angetrieben wurde sie von einem Einzylinder ZDZ 90RV-J. Viel zu schnell wurde sie aber an einen Fliegerkameraden abgegeben, denn die entstehende Lücke konnte mit den verbleibenden zwei und drei Meter-Kunstflugmodellen nie richtig geschlossen werden. Die Modelle um 2,5 m Spannweite sehen in der Luft wie die 3 m-Flieger aus und fliegen eigentlich auch so. Sie sind aber in der Bestückung mit Antrieb und Elektronik bei weitem nicht so aufwendig. Zudem sind sie besser zu transportieren. Als dann ein potentes E-Antriebsset frei wurde, war die Entscheidung für eine neue EDGE 540T schnell getroffen. Sie war bei einem Händler in Deutschland verfügbar und wurde schnell geliefert. Nur mit einem deutlichen Riss in der großen Kabinenhaube. Deren Ersatz sollte leider Monate dauern. Dazu später mehr.
… mit 2,6 m Spannweite und KONTRONIK KSG-Power
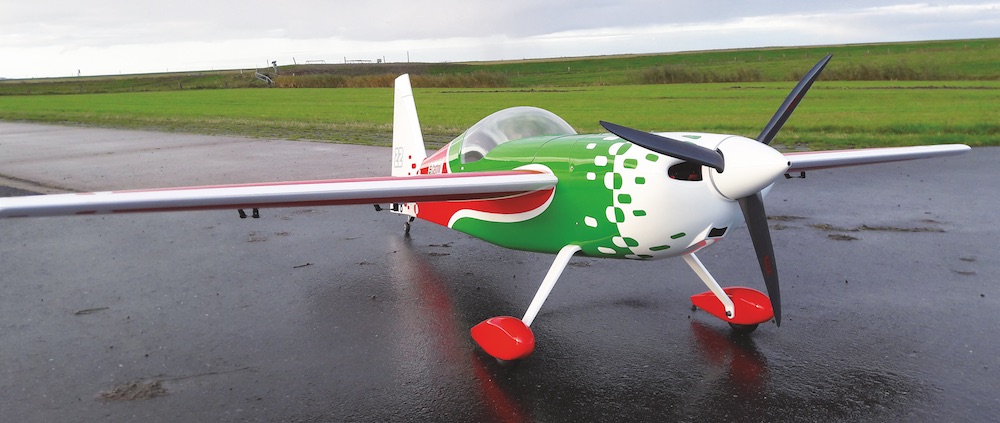
Die Edge 540T gibt es schon eine ganze Weile im Programm von XTreme Composite, sogar in zwei Größen. Nichts Neues also. Die Modelle wurden aber nach Firmenbekunden über die Zeit immer wieder überarbeitet. Stimmt auch, trotzdem gibt es immer noch deutlich Luft nach oben. Wir werden sehen. Der Grundaufbau der Voll-GfK-Kunstflug-modelle ist bei XTreme Composite immer gleich. Es handelt sich um eine Voll-GfK-Konstruktion, als Stützstoff wurde im vorderen Bereich der Rümpfe Herex eingelegt und das Laminat im Vakuumsack getrocknet. Die Edge verfügt im Motorspantbereich zur Verstärkung und besserer Einleitung der Kräfte über diverse Kohlegewebeeinlagen.
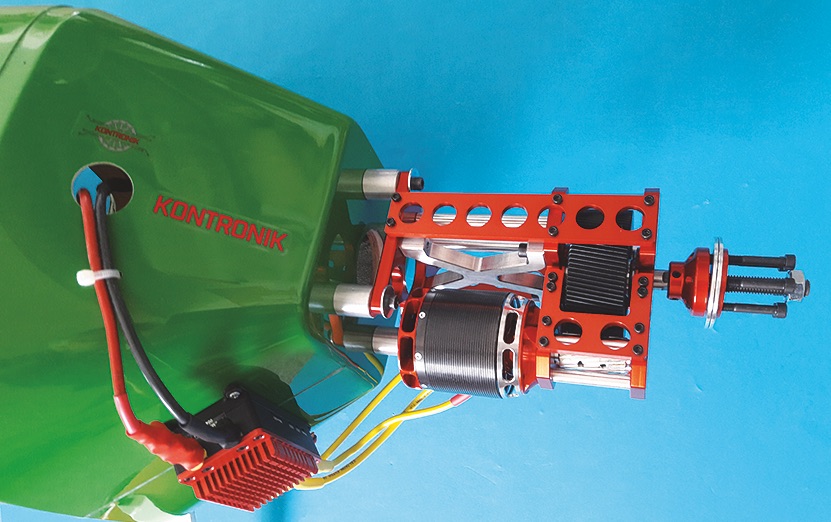
einem ZDZ-Einzylinder angetrieben wurde, kommt nun ein KONTRONIK
KSG E-Antrieb zum Einsatz. Kein Gekleckere mehr, nur noch zwei
Stecker zusammenfügen und startbereit!
Der Motorspant ist fertig eingeharzt, ein üppiges Teil mit 15 mm Dicke. Sämtliche anderen Verstärkungsspanten im Bereich der Fahrwerksaufnahme sind ebenso fertig einlaminiert. Die Seitenstringer bestehen aus GfK-beschichteten 3 mm-Balsaholzstreifen. Sie steifen die Seitenteile des Rumpfs gut aus. Diese Ausführung ist sehr leicht und ausreichend stabil. Qualitätsindiz für die Bauausführung sind die sehr gleichmäßigen Klebefugen aus eingedicktem Epoxidharz und sämtliche feinverschliffenen Kanten der eingebrachten Spanten.
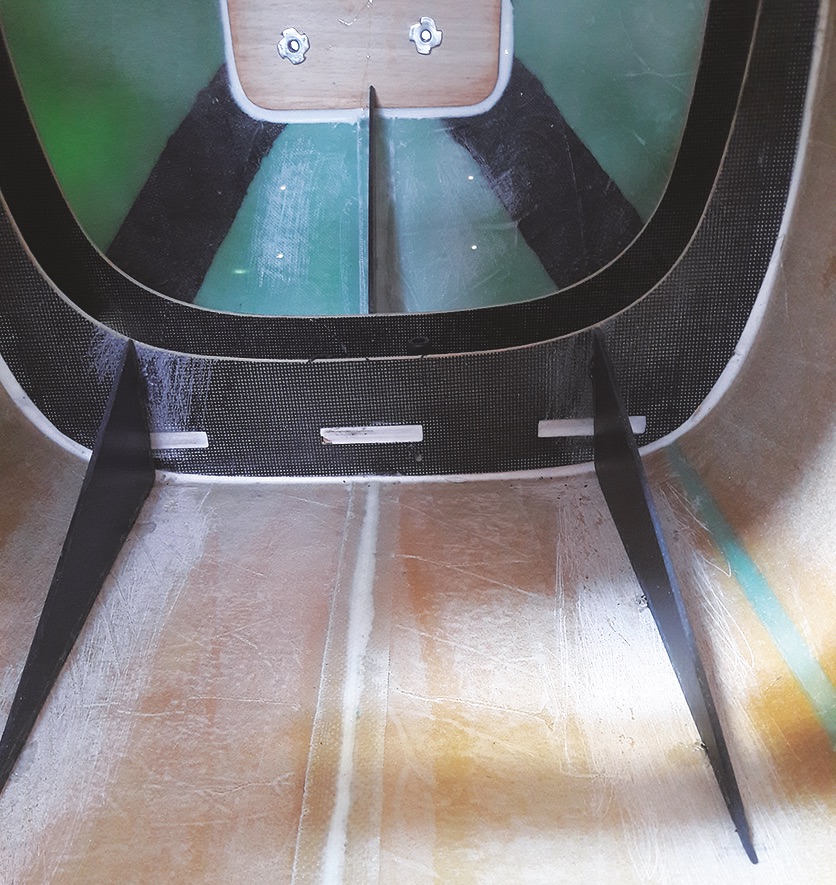
Die gesamte Fahrwerksaufnahme besteht aus mit Kohlegewebe
beschichtetem 3 mm-Flugzeugsperrholz. Alles ist gut in den Rumpf
eingeharzt worden. Zur weiteren Aussteifung wurden aber trotzdem
noch drei Kohlespanten gegen die Fahrwerksaufnahme geklebt.
So wird sie noch besser abgestützt und auftretende
Kräfte besser in den Rumpf abgeleitet.
Für die Aufnahme der Fahrwerksschenkel wurde kohlebeschichtetes 3 mm-Flugzeugsperrholz verwendet. Das Aufnahmegerüst ist sauber in den Rumpf eingeharzt; trotzdem wurden noch drei Abstützungen aus Kohlegewebeplatten in Längsrichtung vor und hinter das Trägergerüst geharzt, um auch Kippneigungen besser auffangen zu können. Das Fahrwerk selbst besteht aus zwei Kohle / GfK-Schenkeln, die jeweils seitlich in den Rumpf in fertig ausgenommene Schlitze eingesteckt werden. Im Inneren werden sie mit vier Stahlschrauben verschraubt. Die Vorbereitung der Aufnahmen mit fertig eingelassenen Einschlagmuttern und die passgenauen Schlitze sind nur auf den ersten Blick hilfreich; die Verschraubung selbst ist eine reine Fummelei.
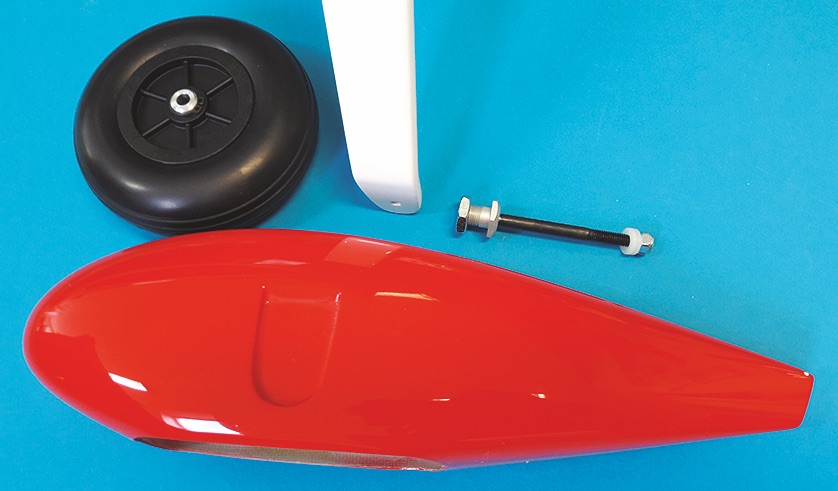
Sie werden in zwei fertig eingefräste Schlitze seitlich in den Rumpf gesteckt
und innen verschraubt. Toll sind die ausgeformten Sicken in den Radverkleidungen,
in die die Fahrwerksschenkel eingreifen.
Die Fahrwerksschenkel verfügen noch nicht über die entsprechenden Löcher zur Durchführung der Schrauben. So muss man zunächst eine Bohrschablone mit den Maßen der Aufnahmebretter inkl. der exakten Positionen der Muttern fertigen. Danach werden dann die Fahrwerksschenkel gebohrt und verschraubt. Ok, das geht auch, ist aber sehr umständlich. Viel besser wäre es, gleich in der Fertigung die Löcher mit aufgesetzten Fahrwerksschenkeln zu bohren. Dann passt alles sofort. Wird ein Benzinmotor als Antrieb eingesetzt, l

zum Einsatz, um die Kraft des Antriebes auch umsetzen zu können.
Die Kohlepropeller 25,5 x 12 und 26 x 12 von Elster Modellbau haben sich bewährt.
iegen später der oder die Schalldämpfer genau über diesen Verschraubungen, ein schnelles Abnehmen des Fahrwerks ist damit unmöglich. Besser wäre es auch, die Verschraubungen von unten unter dem Rumpf auszuführen. Da gilt es also noch nachzuarbeiten. Apropos Fahrwerk: Die beiliegenden Radverkleidungen sind perfekt auf die Fahrwerksschenkel abgestimmt. Sie verfügen über seitlich eingearbeitete Sicken, in die sich die Fahrwerksschenkel einschmiegen und einen sicheren Halt der Verkleidungen sicherstellen. Tolles Detail.
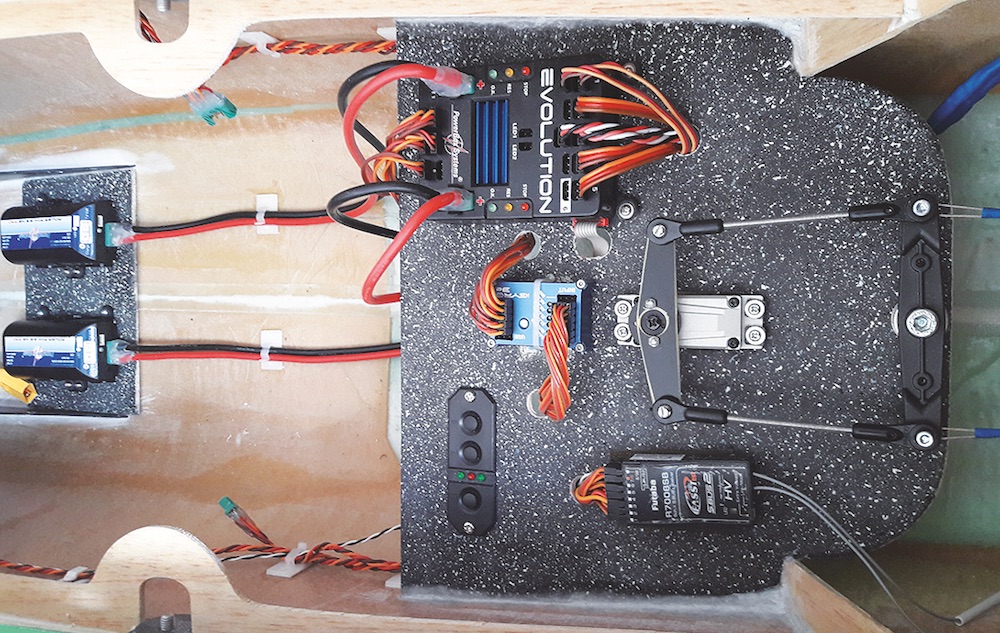
die RC-Komponenten und Antriebsakkus problemlos eingesetzt werden.
Es gibt auch Raum genug, um mit einer geschickten Positionierung der
Komponenten den Schwerpunkt exakt einzustellen.
Die beiliegenden langen Gewindeschrauben sollten als Achsen verwendet werden. Das geht, ist aber nicht wirklich schön. Neue Achsen stammen von FEMA. Sie können auf der einen Seite der Fahrwerksschenkel ordentlich verschraubt und zudem noch auf der gegenüberliegenden Seite mit einem Gegenlager versehen werden. So wird die gesamte Konstruktion auch noch schön gestützt. Als Räder kommen …