Das Original
Die Entwicklung der Bölkow Bo 208 Junior geht auf das Amateurbauflugzeug BA-7 von Björn Andreasson zurück. Dieser entwarf neben seiner Tätigkeit bei Convair in San Diego die in Ganzmetallbauweise hergestellte und als Schulterdecker mit drei Grad nach vorne gepfeilten Tragflächen ausgelegte BA-7. Die Spannweite betrug 7,15 m. 1960 kehrte Björn Andreasson nach Schweden zurück, wo er bei Malmö Flygindustri (MFI) die Stelle des Chefkonstrukteurs übernahm. Seine BA-7 brachte er mit und überarbeitete die Konstruktion für die Serienfertigung. Die Bölkow GmbH erwarb 1961 die Lizenz für den Bau des MFI-9 Junior. Die Bo 208 Junior wurde leicht abgewandelt, so wurden ein gerades statt eines geknickten Bugfahrwerks, ein neues Ruder und eine modifizierte Kabine eingebaut. Auf der Luftfahrtschau 1962 in Hannover wurden die ersten beiden in Deutschland gebauten Bo 208 ausgestellt.
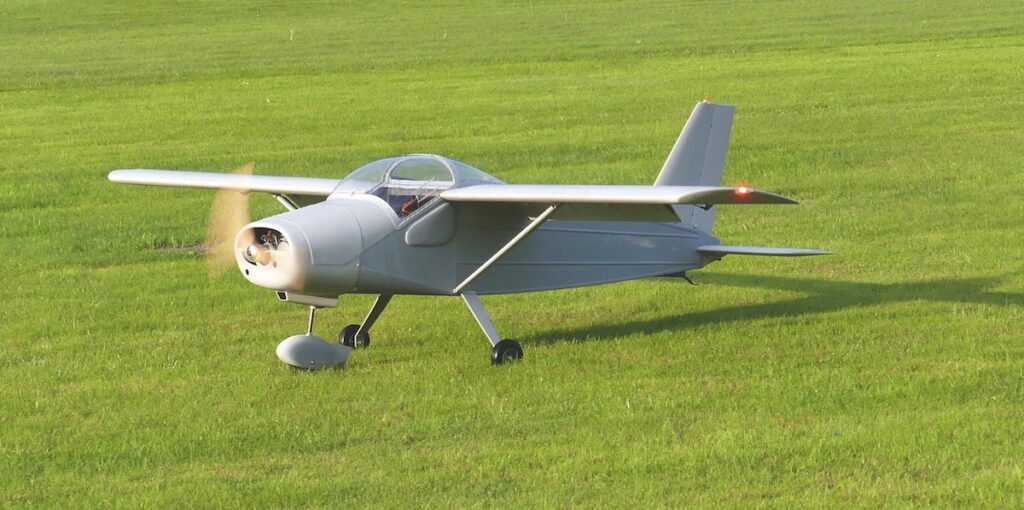
Eine Idee wird Wirklichkeit
In einer gemütlichen Runde nach einem schönen Flugtag entstand die Idee, ein Flugzeug im Rahmen eines Gemeinschaftsprojekts zu bauen. Als unser Fliegerfreund Manfred wieder einmal von seiner originalen Junior schwärmte, stand es für uns fest: Wir bauen eine Bölkow Junior. Es war geplant, vier Modelle im Maßstab 1:2,8 zu bauen. Jeder der Teammitglieder bringt seine Fähigkeiten mit ein und das Modell sollte als kompletter Eigenbau entstehen.
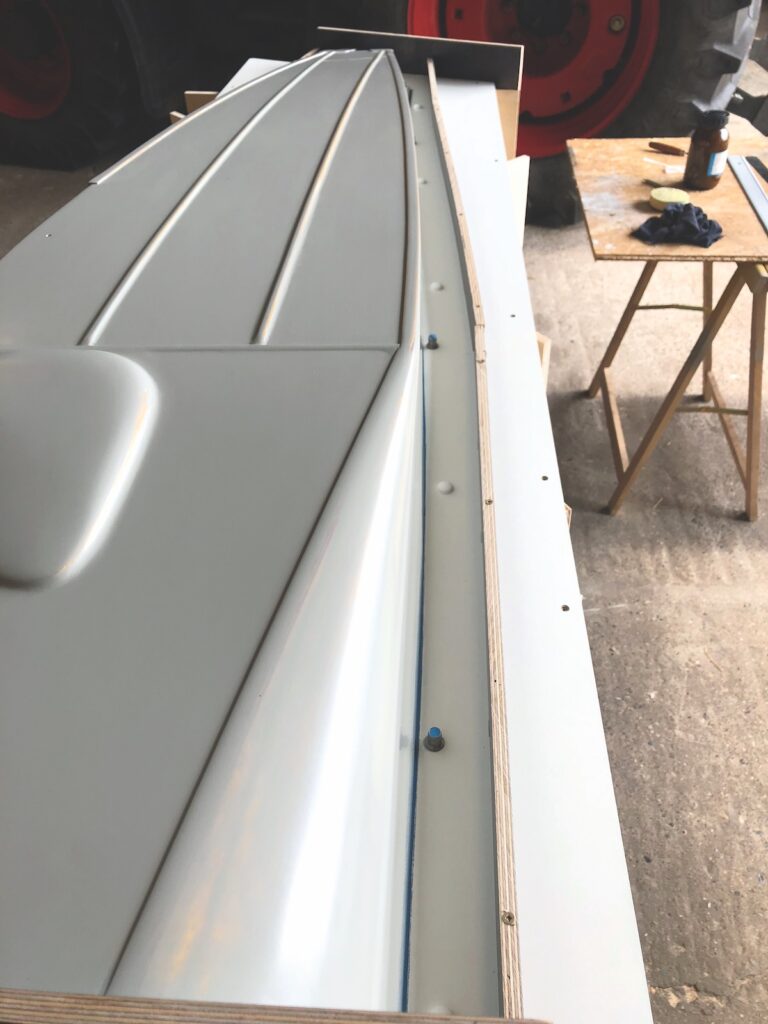
Rumpf und Formenbau
Nach einer Phase der Planung und einigen Recherchen im Internet konnte mit dem Bau begonnen werden. Eine Drei-Seiten-Ansicht aus der MFI von Herrn Fischer bildete die Grundlage. Der Autor dieses Berichts übernahm die Aufgabe, alle Formen für das Modell herzustellen. Es entstanden Urmodelle aus Holz für den Rumpf, die Motorhaube, Randbögen, Kabinenrahmen und die Radverkleidungen. Die Bearbeitung der Holzurmodelle endete mit einer Versiegelung aus 25 g-Glasgewebe und Topfit von Ralf Petrausch. Zuvor wurden noch einige Details am Rumpf angebracht, wie z.B. die Batterieklappe, Sicken am Rumpf und die Beulen im Cockpitbereich für die Schultern der Piloten. Die Teile wurden anschließend alle mit Füller bearbeitet und geschliffen.
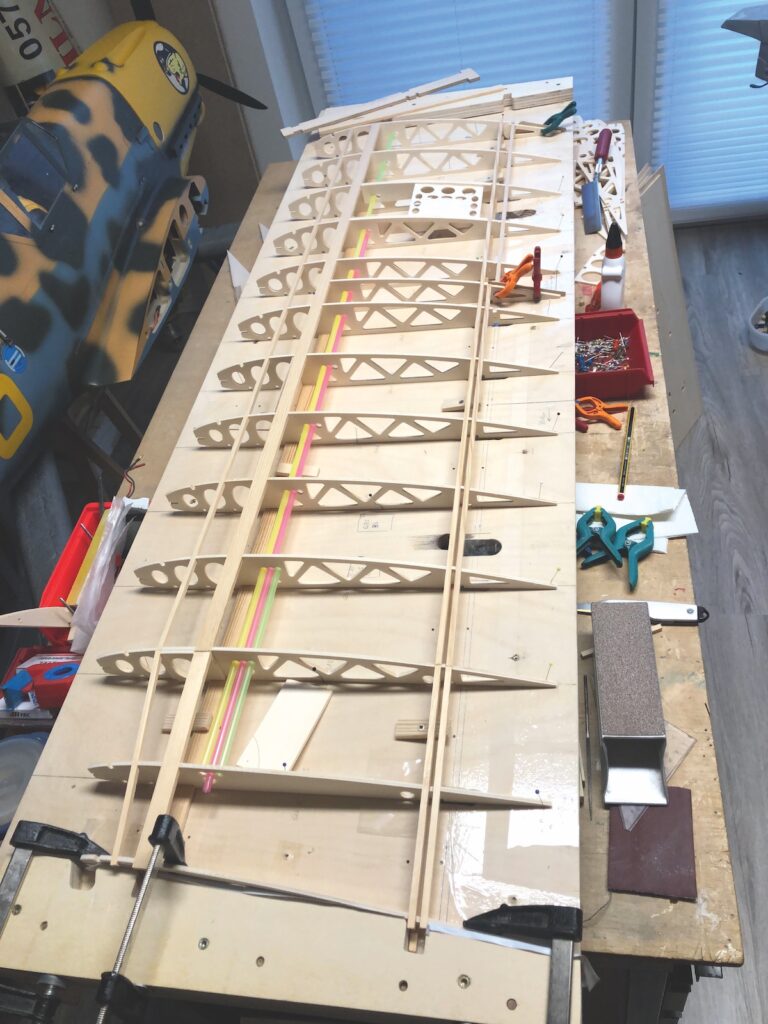
Diese Oberfläche reichte für unseren Zweck aus und die Ergebnisse konnten sich sehen lassen. Das Seitenruder wurde in Wabensandwichbauweise hergestellt. Es war der erste Versuch und für mich eine neue Technik. Es entstand ein leichtes, aber sehr festes Seitenleitwerk. Die Rumpfform sah keinen festen Motorspant vor, da jeder der Teammitglieder einen anderen Antrieb verwenden wollte. Nach der üblichen Arbeit zum Formenbau entstanden dann im Laufe der Zeit vier Rümpfe, Motorhauben, Randbögen und auch Rahmen für das Cockpit.
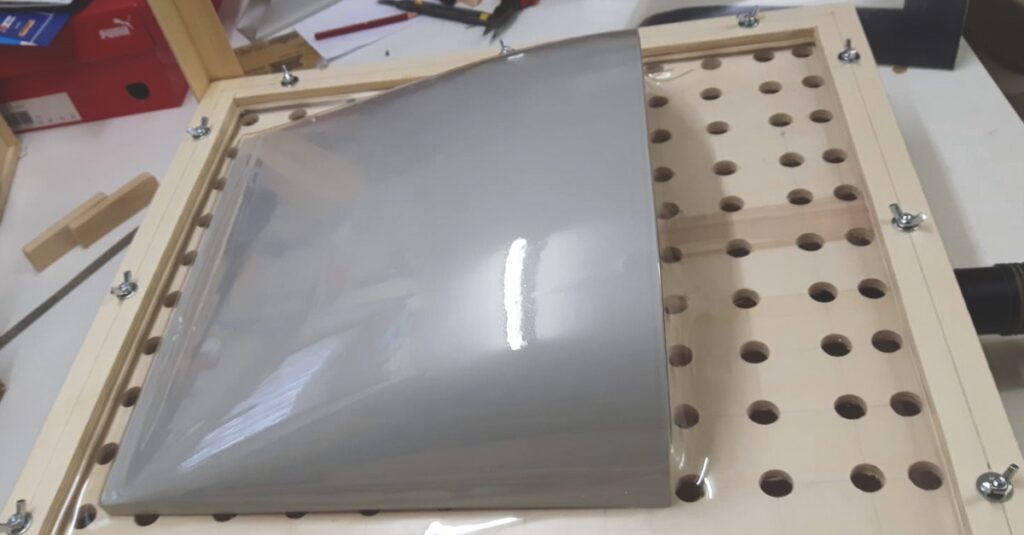
Tragflächen und Leitwerk
Das Flugzeug ist auch im Original sehr einfach aufgebaut. Deshalb konnte mein Clubkamerad Jan schon unabhängig von der Fertigstellung des Rumpfs die Tragflächen zeichnen und für seine Fräse vorbereiten. Irgendwann stand er an meiner Tür und sagte: »Ich habe die Rippen fertig!« Ein Karton voller sauber gefräster Rippen aus 3 mm-Pappelsperrholz. Dazu gehörten auch alle Lager für die Ruder und Servohalterungen. Gleichzeitig hatte er eine Helling gebaut, die geeignet war, den rechten und linken Tragflügel, mit drei Grad Vorpfeilung und V-Form in traditioneller Holzbauweise, verzugsfrei aufzubauen. Die Tragflächen wurden mit 1,5 mm-Balsaholz beplankt und mit einer 40 g-Glasmatte beschichtet. Die Tragflächen passten genau an den Rumpf. Flächenaufnahme und EWD wurden schon am Urmodell eingemessen und markiert.
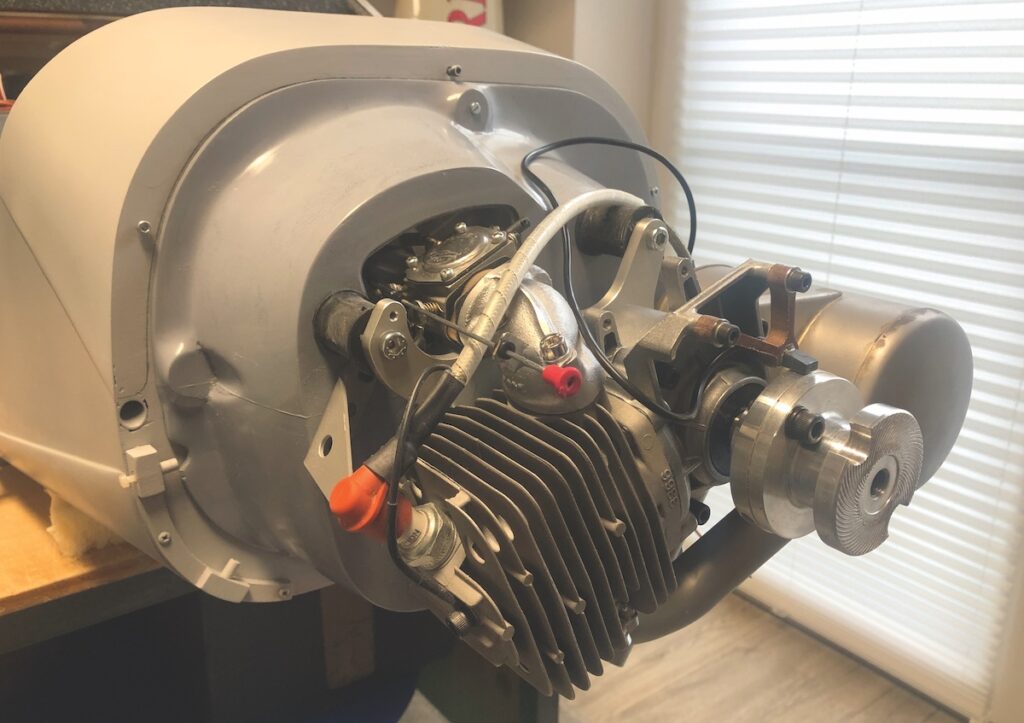
Herausforderung Kabinenbau
Mein Bruder Siegfried hatte die Aufgabe übernommen, Kabinenhaube und Höhenruder zu bauen. Die Wartezeit für Rumpf und Frästeile überbrückte er mit dem Bau einer geeigneten Tiefzieheinrichtung. Nach Fertigstellung des Rumpfs baute ich die Formen der zweiteiligen Kabinenhaube. Nach einigen Fehlversuchen entstanden brauchbare …
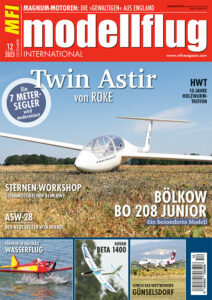