Seit einiger Zeit begleiten wir Karl-Heinz Vögeli beim Bau seines Superscale-Modells Pfalz D.IIIa. Besonders wichtig ist ihm dabei, auch in den kleinsten Details so nah wie möglich am Original zu bleiben. Dazu hat er sich einige geniale Lösungen einfallen lassen, von denen er uns in den beiden vorangegangenen Berichten schon einige verraten hat. Inzwischen hat das Projekt sehr große Fortschritte gemacht und die Pfalz D.IIIa steht mittlerweile auf eigenen Beinen.
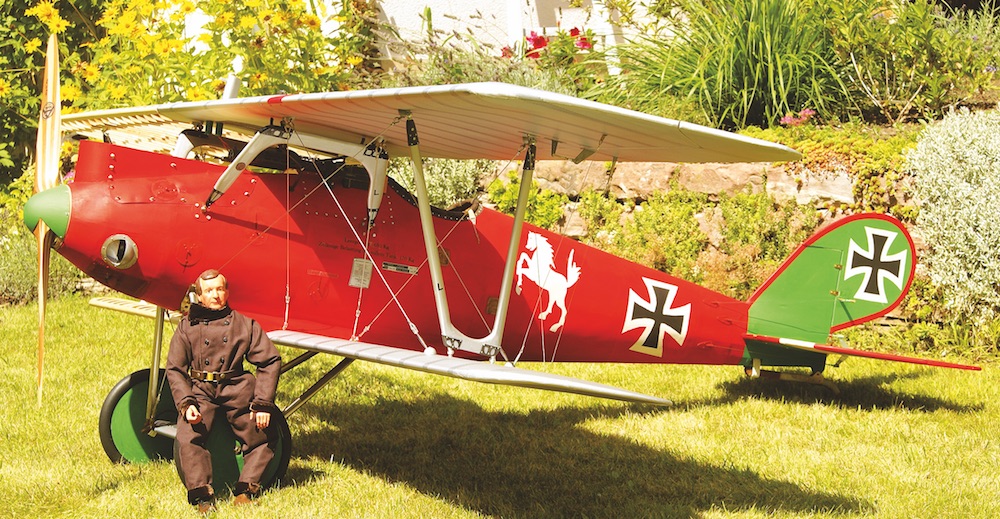
Dazu wurde der Kopf des Erbauers eingescannt und mit dem 3D-Drucker erstellt.
Die Pfalz steht auf ihren eigenen Füssen
Seit einiger Zeit begleiten wir Karl-Heinz Vögeli beim Bau seines Superscale-Modells Pfalz D.IIIa. Besonders wichtig ist ihm dabei, auch in den kleinsten Details so nah wie möglich am Original zu bleiben. Dazu hat er sich einige geniale Lösungen einfallen lassen, von denen er uns in den beiden vorangegangenen Berichten schon einige verraten hat. Inzwischen hat das Projekt sehr große Fortschritte gemacht und die Pfalz D.IIIa steht mittlerweile auf eigenen Beinen.
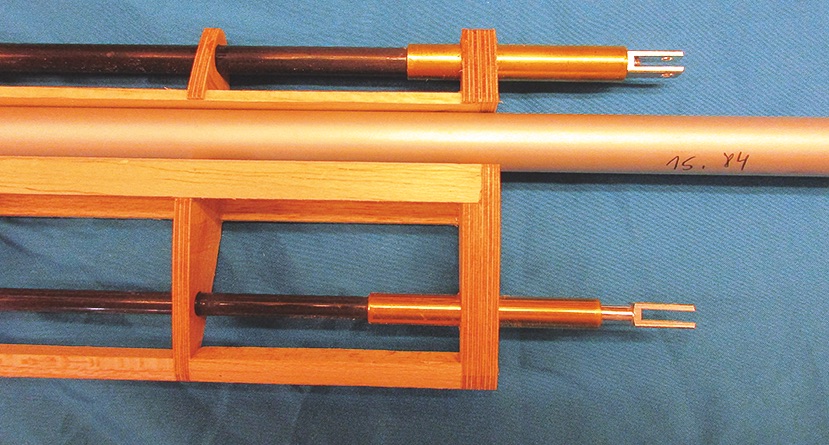
ist mit Gabelköpfen befestigt.
In meinem dritten Bericht über den Bau der Pfalz D IIIa möchte ich über den Baufortschritt und über die einzelnen Details des Modells berichten. Beim Baldachin sind jetzt nicht nur der Flächenkühler und der Tragflächentank, sondern auch die Unterseite mit der Kühler-Abdeckung und Schubstange fertig. Was ich aber sehr bedauere, ist dass mit der Bespannung auch die ganzen Details, die in der Fläche verbaut wurden nicht mehr zu sehen sind. Bei der oberen Tragfläche dominieren natürlich die Hebel der Querruderanlenkung und die großen Kreuze das Bild auf der Fläche.
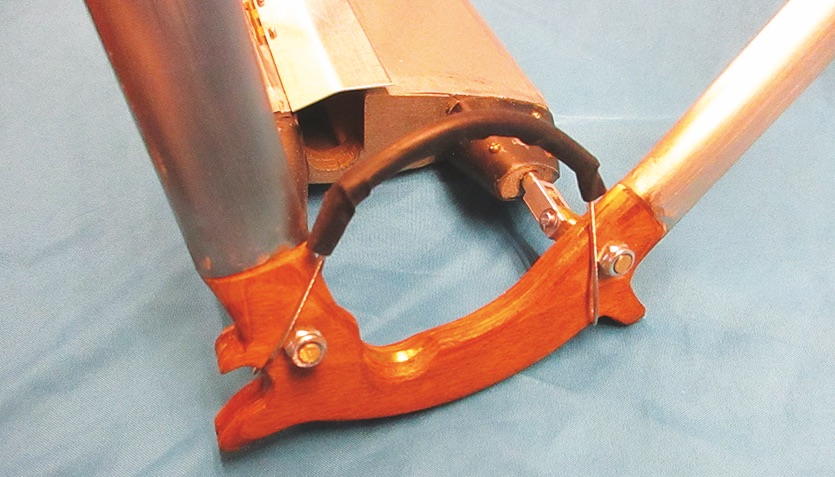
begrenzt das Durchfedern der Achse.
Fahrwerk
Das Fahrwerk besteht aus den einzelnen Komponenten: Bauhelling zum Aufbau der einzelnen Komponenten; Höhenflosse des Fahrwerks; Fahrgestellsbügeln (Streben); Radachse und den Rädern.
Bauhelling
Zum Aufbau der einzelnen Komponenten habe ich eigens ein Baubrett angefertigt. Dazu habe ich die Unterseiten der Spanten 3 bis 7 noch mal neu gefräst und im genauen Abstand auf ein Baubrett montiert. Anschließend wurden an alle vier Seiten des Baubretts Kanthölzer hochkant verschraubt. Diese Hölzer dienen zur Aufnahme der Fahrwerksstreben, um diese genau in Höhe, Seite und mit den entsprechenden Anstellwinkeln auszurichten. Auch dienten die Hölzer zur Auflage der Höhenflosse mit ihren Hilfsachsen.
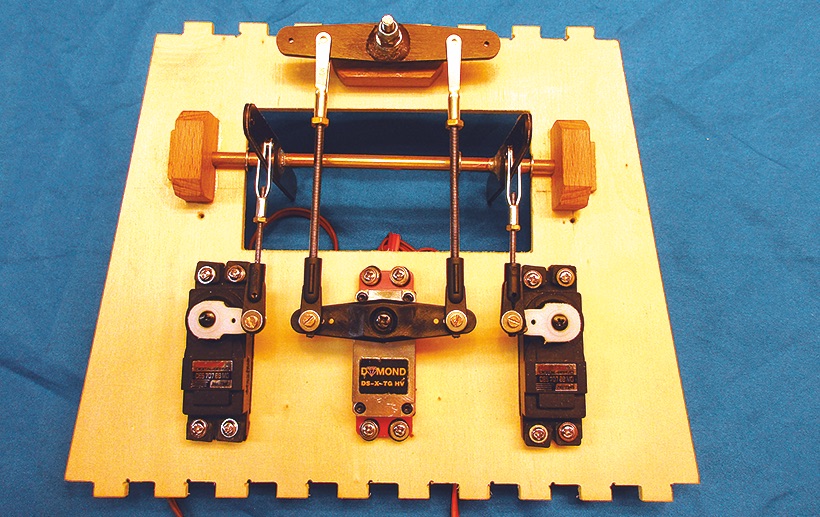
MFI 11 / 2017 nochmal neu angefertigt.
Höhenflosse
Zwischen den V-förmigen Streben liegt die tropfenförmig ausgeführte Höhenflosse. Die Enden der Höhenflosse ruhen im Original in Stahlblechschuhen und sind mit den Streben verschraubt. Oberhalb der Fahrwerksachse ist eine Aluminiumklappe montiert, die beim Durchfedern der Achse nach oben ausschwingen kannn. Im Modell habe ich die Befestigung der Höhenflosse an den Streben mit Gabelköpfen ausgeführt. Damit das Alublech an der Oberseite der Höhenflosse ausschwingen kann, wurde es mit vier Scharnieren verschraubt. Die beiden Hilfsachsen vor und hinter der Radachse, die mit den Streben verschraubt werden, habe ich mit Kohlfaserrohren ausgeführt und zur Verstärkung eine Gewindestange eingeschoben. Dies hat auch der Vorteil, dass ich damit die Breite der Flosse einstellen konnte.
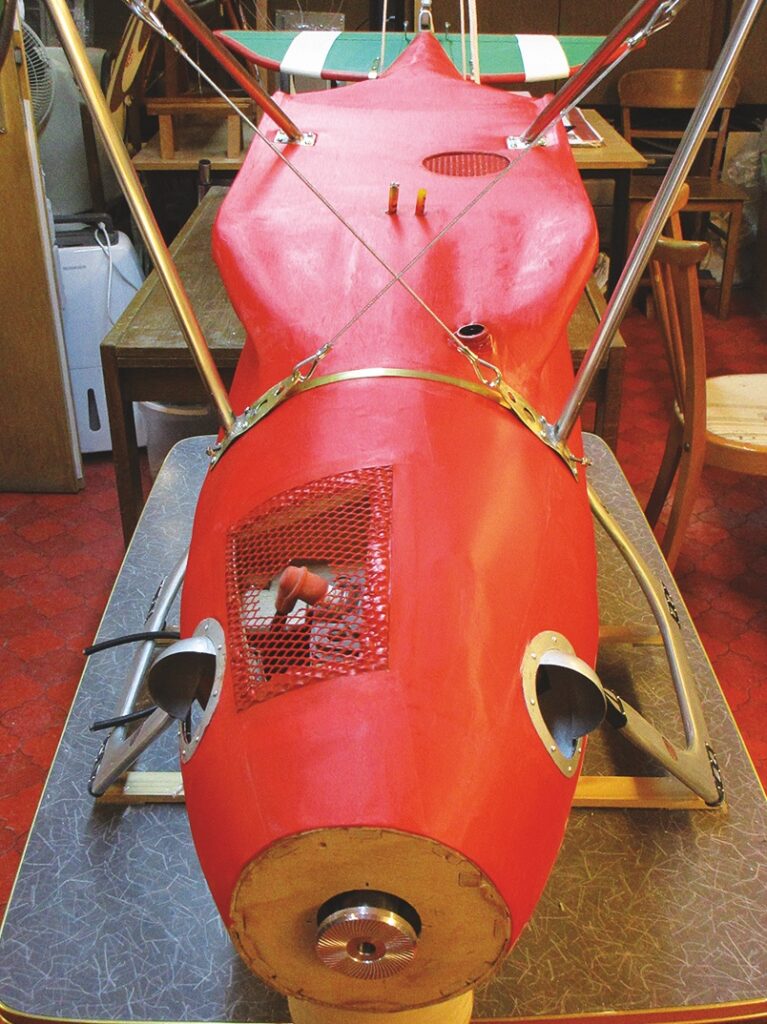
Zur weiteren Verstärkung der Flosse sind links und rechte Messinghülsen über die Kohlefaserrohre geschoben. Ich denke, diese Verstärkungen sind notwendig, denn die vier Haltepunkte müssen immerhin die Landungsstöße eines fast 25 kg schweren Modells aufnehmen. Die sich seitlich der Höhenflosse befindlichen Stahlblechschuhen wurden mit Tiefziehteilen nachgebildet. Die Verbindung von Höhenflosse und Streben erfolgt wie im Original mit Gabelköpfen und Bolzen.
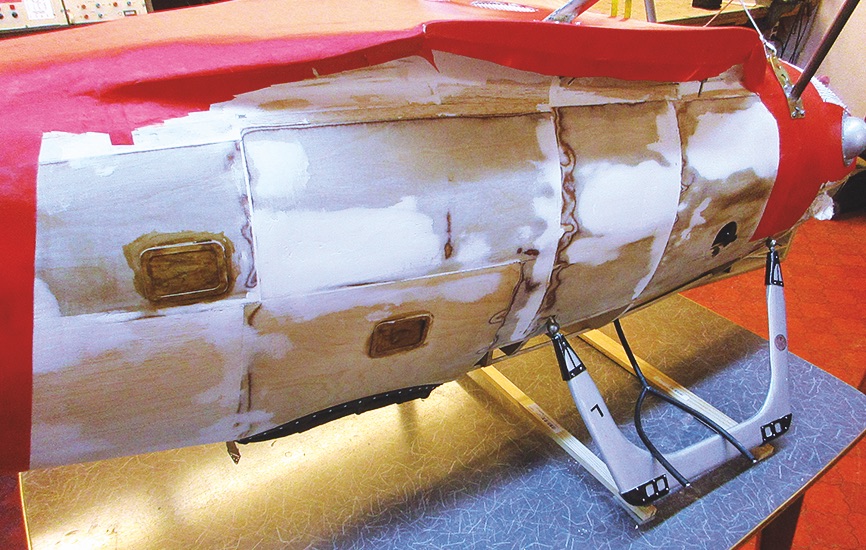
geschliffen ist, wird er mit Oratex bespannt werden.
Radachse
Die Radachse besteht aus einem Aluminiumrohr mit 16 mm Durchmesser. In dieses Rohr wurden acht Nadellager mit einem Außendurchmesser von 14 mm und Innendurchmesser 10 mm eingesetzt. Die eigentliche Achse besteht aus zwei Messingrohren, die ineinander geschoben wurden. Durch die in das Alurohr eingeschobenen Nadellager ergibt sich ein guter Rundlauf der Räder. Um ein seitliches Verschieben der Achse, die ja nur durch die Gummibänder gehalten wird, zu vermeiden, habe ich in das Alurohr links und rechte zwei kleine 0,3 mm-Rillen auf der Drehbank eingedreht. In diese Rillen wurde ein Wellensicherungsring aufgezogen. Der Ring wurde seitlich der Rippen in die Höhenflosse eingefügt. Damit ist ein seitliches Verschieben der Radachse gegenüber der …
Einen ausführlichen Bericht lesen Sie in der Ausgabe 12/2020 des MFI Magazins.